Metal
Copper film is grown by electrodeposition into the Damascene pattern to fabricate copper interconnect of integrated circuits. Therefore, a continuous copper seed layer with good step coverage is essential for a high quality electrodeposition. Traditionally, the copper seed layer has been manufactured using ionized physical vapor deposition (iPVD) technique. However, as the feature sizes decrease, i-PVD will soon face scaling problems. ALD is an ideal solution to deposit highly conformal seed layer due to its self-limiting growth characteristics.
In our study, highly conformal copper seed layer prepared by deposition of copper film by alternating exposures to copper precursor and H2 [1]. The copper precursor that used is bis(1-dimethylamino-2-methyl-2-butoxy)copper(II) [Cu(dmamb)2].
The films were prepared mainly on air-exposed ALD Ru (30 nm)/SiO2 (100 nm)/Si wafers. ALD ruthenium film was prepared using (2,4-dimethylpentadienyl) (ethylcyclopentadienyl)ruthenium [Ru(DMPD)(EtCp)] and O2 at 280 °C.
-
J. Park, K. Jin, B. Han, M. J. Kim, J. Jung, J. J. Kim, and W. Lee, “Atomic layer deposition of copper nitride film and its application to copper seed layer for electrodeposition,” Thin Solid Films, vol. 556, pp. 434–439, 2014.
Metal Oxides
Cobalt Oxide
Cobalt oxide thin films have been investigated extensively because of their applications in various technology fields, such as electrochromic devices, heterogenous catalysts, solid state gas sensors, RERAM devices, and intercalation compounds for energy storage.
ALD of cobalt oxide films was studied using different organometallic cobalt compounds, such as dicobalt hexacarbonyl tert-butylacetylene [C12H10O6(Co)2, CCTBA] and cyclopentadienylcobalt dicarbonyl [(C5H5)Co(CO)2, CpCo(CO)2].
Film growth and reaction of the cobalt precursor during ALD studied using in situ quartz crystal microbalance (QCM).
-
B. Han, J.-M. Park, K. H. Choi, W.-K. Lim, T. R. Mayangsari, W. Koh, and W.-J. Lee, “Atomic layer deposition of stoichiometric Co3O4 films using bis(1,4-di-iso-propyl-1,4-diazabutadiene) cobalt,” Thin Solid Films, vol. 589, pp. 718–722, 2015.
-
B. Han, K. Ha Choi, J. Min Park, J. Woo Park, J. Jung, and W.-J. Lee, “Atomic layer deposition of cobalt oxide thin films using cyclopentadienylcobalt dicarbonyl and ozone at low temperatures,” J. Vac. Sci. Technol. A Vacuum, Surfaces, Film., vol. 31, p. 01A145, 2013.
-
B. Han, K. H. Choi, K. Park, W. S. Han, and W.-J. Lee, “Low-Temperature Atomic Layer Deposition of Cobalt Oxide Thin Films Using Dicobalt Hexacarbonyl tert-Butylacetylene and Ozone,” Electrochem. Solid-State Lett., vol. 15, no. 2, p. D14, 2012.
![]() cobalt oxide 2.pngMass change during an ALD cycle consisted of a CpCo(CO)2 pulse, a purge, a O3/O2 pulse, and a purge. The m1 is the mass change during a cobalt precursor pulse and the m0 is the mass increment after a complete ALD cycle. Exposure of CpCo(CO)2 and O3/O2 were 2106 and 5108 L, respectively. Won-Jun Lee Sejong University 이원준 세종 대학교 | ![]() cobalt oxide.pngCross-sectional TEM images of ALD cobalt oxide films on trench-patterned wafers deposited at (a) 50 C, (b) 100 C, and (c) 150 C. Exposures of CpCo(CO)2 and O3/O2 were 2106 and 5108 L, respectively. The thickness of all cobalt oxide films was 3 nm. Won-Jun Lee Sejong University 이원준 세종 대학교 |
---|
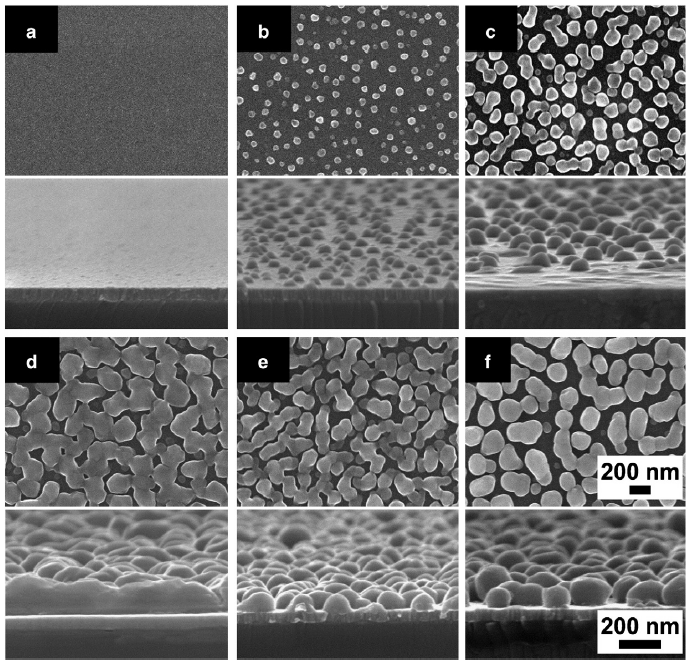
Plan view and bird's-eye view SEM photographs of the copper films prepared using alternating exposures to Cu(dmamb)2 and H2: (a) ALD ruthenium substrate; the copper film deposited at (b) 120°C, (c) 140°C, (d) 160°C, (e) 180°C and (f) 200°C. Won-Jun Lee Sejong University 이원준 세종 대학교
Nitrides
In our study, the preparation of copper films by reduction of copper nitride film method was conducted by ALD-copper nitride film using Cu(dmamb)2 and ammonia. The growth of copper nitride film was monitored in situ during ALD using a quartz crystal microbalance (QCM) system.
The ALD copper nitride film shows smooth surface and excellent step coverage of >98% as shown in figure below.
-
J. Park, K. Jin, B. Han, M. J. Kim, J. Jung, J. J. Kim, and W. Lee, “Atomic layer deposition of copper nitride film and its application to copper seed layer for electrodeposition,” Thin Solid Films, vol. 556, pp. 434–439, 2014.

Cross-sectional TEM images of ALD copper nitride films on trench patterns (aspect ratio ~7). Won-Jun Lee Sejong University 이원준 세종 대학교

SEM photographs of the surfaces of the ALD copper nitride films deposited at (a) 100°C, (b) 120°C, (c) 140°C and (d) 160°C. Won-Jun Lee Sejong University 이원준 세종 대학교